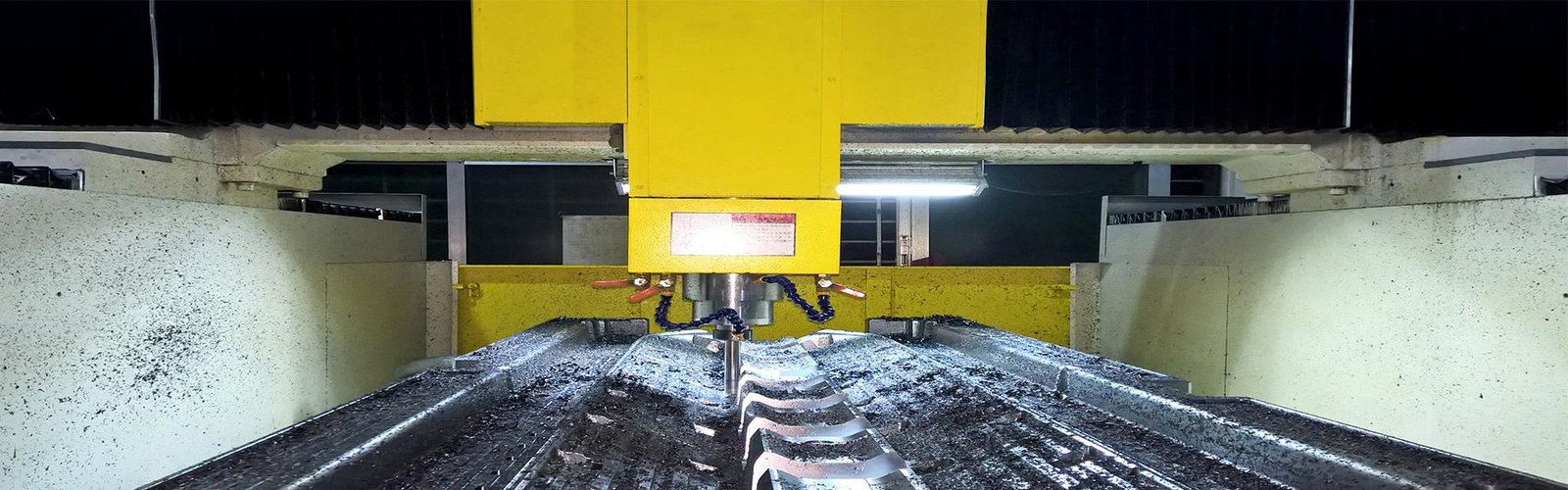
New Trends In Injection Mold Technology
With the diversification and personalization of social needs, as well as the wide application of many new materials and new processes, the structural forms and cavity requirements of modern molds are becoming more and more complex. It is imperative to develop and develop new mold design and manufacturing technologies.
Injection mold companies no longer only focus on the competition of homogenized low-cost mold technology, but more and more attention to the user’s individualization and complex and difficult needs. Such as transfer custom mold technology, laminated mold, two-color double material mold, high-gloss injection mold, micro-foaming mold, etc., the mold structure is novel, the technology is mature, and the application is more and more extensive.
For example, in terms of micro-foaming, Yizumi Company first introduced the FoamPro foaming process on CHINAPLAS last year. The innovative SmartClamp intelligent clamping system independently controls the pressure and position independently through four guide columns, which can automatically correct and parallel the template parallelism. Accuracy reaches ±0.015mm/2ms, and through the foaming precision mold opening technology (Breathing Mold), the cavity volume is increased synchronously during the foam molding process, effectively eliminating the potential internal stress and trapping problem of the product, and foaming the product. The effect is better, and the product wall thickness is uniform, and the precision and surface quality of the foaming product are improved. At the same time, the FoamPro micro-foaming solution is equipped with the FLEXflow servo needle valve hot runner system developed by HRSflow Plastic Flow Channel Company of Italy. It is driven by servo motor and can precisely adjust the needle valve speed, valve opening size and valve opening and closing sequence. Product molding defects, such as weld lines, and stress, warpage, etc. caused by imbalance of the runner.